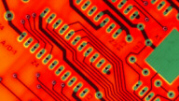
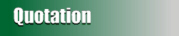
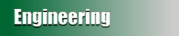
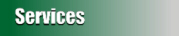
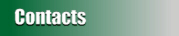
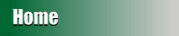 |
Download our FREE Microwave Laminates Comparison Chart. Makes
a great reference tool for engineers.
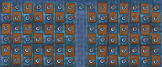
|
Single-sided PCB
Single-sided printed circuits represent the
least sophisticated (and thereby least costly) of the printed circuit
products. These boards usually do not require plated through holes and
only have a circuit pattern on 1 side. Quite often single-sided boards
are referred to 'punch and crunch' due to the fact that high volume runners
are profiled with tool and die. |
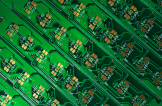
|
Double-sided PCB
Double-sided printed circuits are a step above single-sided in their complexity. Double sided PCBs require plated through
holes to provide better anchoring for soldered components and front to back
electrical continuity. Most designs require soldermask front and back
along with a silkscreen layer for component designators. Very often
double sided designs utilize a mixed technologies of through hole (PTH) and
surface mount (SMT). |
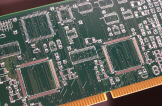
|
Multilayer PCB
Multilayer printed circuits consist of 3 or more circuit
layers bonded together by a thickness of insulating material called prepreg.
Prepreg is B stage epoxy impregnated fiberglass. Multilayers are
generally considered to be the most sophisticated printed circuit product
due to their construction methods and design complexities. |
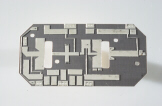
|
RF/ Microwave
Most RF PCB designs are considered to be functional
components of the assembled sub-system. These designs
utilize various patterns in the circuitry to achieve changes in the characteristics of the
RF energy
field. Tight line width tolerances and front to back registration are considered to be the rule when
fabricating these PCBs. Exotic materials such as: PTFE, Duroid, and
ceramics are often utilized for their stability and dielectric properties. |
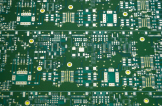
|
SMOBC-HAL (surface
mount technology SMT)
Soldermask Over Bare Copper usually provided with a Hot Air Level (HAL)
solder finish which selectively places solder onto pads and holes only.
This provides an excellent base for attaching SMD components. |
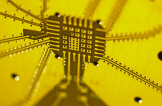
|
Alternative Finishes (Including RoHS Compliant Finishes)
We offer a variety of
different surface finishes including: Gold, nickel, tin, solder reflow,
bare copper with anti-oxidant, silver, and rhodium. Thicknesses
can vary according to your specification (see
Engineering for default thicknesses). |
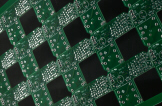
|
Panelization Options
We
can provide accurate scored and/or routed arrays to optimize your
assembly process. Typically, an 8" x 10" panel is the most cost
effective size due to 'best yield' from our standard panel size. |
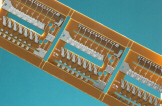
|
High Performance
Laminates
From multifunctional epoxy
resin systems to high performance polyimide, we offer a wide
selection of laminates (see
Laminates). Some of the
multifunctional epoxies are approaching polyimide in high temperature
performance. |
Manufacturing Capabilities:
Layers: |
1-12 FR4, polyimide, multifunctional, and multilayer RF |
Lines/Spacings (mils): |
6/6 production, 4/4 prototype |
SMT minimum pitch (mils): |
18 |
Minimum finished hole size (mils): |
10 |
Aspect ratio (max.): |
6:1 |
Blind / Buried vias |
yes, with some restrictions |
Available finishes: |
SMOBC-HAL, solder reflow,
electroless tin (20-30 µi),
immersion tin (10-15
µi) , nickel, gold,
bare copper (with CU-56 antioxidant), immersion silver. |
Soldermasks: |
Liquid Photoimageable (LPI). |
Soldermask Colors: |
green, blue, red, black, clear |
Silkscreen |
Liquid Photoimageable, epoxy based thermal cure. |
Silkscreen Colors: |
white, yellow, black |
Minimum LPI Mask Resolution (mils): |
4 |
Copper Foil: |
minimum 1/2 oz., maximum 3oz with mask or silk - 5oz without mask or
silk |
Electrical Test: |
grid test or flying probe netlist testing |
Laminate Thicknesses: |
0.005"
- 0.250" |
Lead Times: |
single-sided protos - 24-48 hrs.
double-sided protos - 48-72 hrs. (includes RF boards)
quickturn single and double-sided - 5 days
multilayer protos - 5-10 days
normal lead times - 2-3 wks
note: lead times are calculated from the time the PO is received to
the time the product is shipped. If the PO (and gerber files)
are received by Noon we will count that as day one. |
Line width etching tolerances |
1/2 oz. foil - +/- .001", 1 oz foil - +/- .002" |
Special Processes: |
peelable soldermask |
Panel sizes: |
min - 6" x 9", max - 18" x 24" |
QA / Testing: |
Quality system compliant with ISO 9000, inspection to IPC-A-600
(current rev.) Class 2, solderability testing to IPC-TM-XXX,
electrical test, cross-sectioning lab, coating thickness testing, PTH
thickness testing, calibration system to MIL-STD-45662, UL-94V0 (94V1
for polyimide). |
|
home
|
profile
| products
| services
| laminates
| processes
| engineering
|
rfq |
contacts
|
circuits@standardpc.com
© 2002, 2007 by Standard Printed
Circuits Inc.
All Rights Reserved |